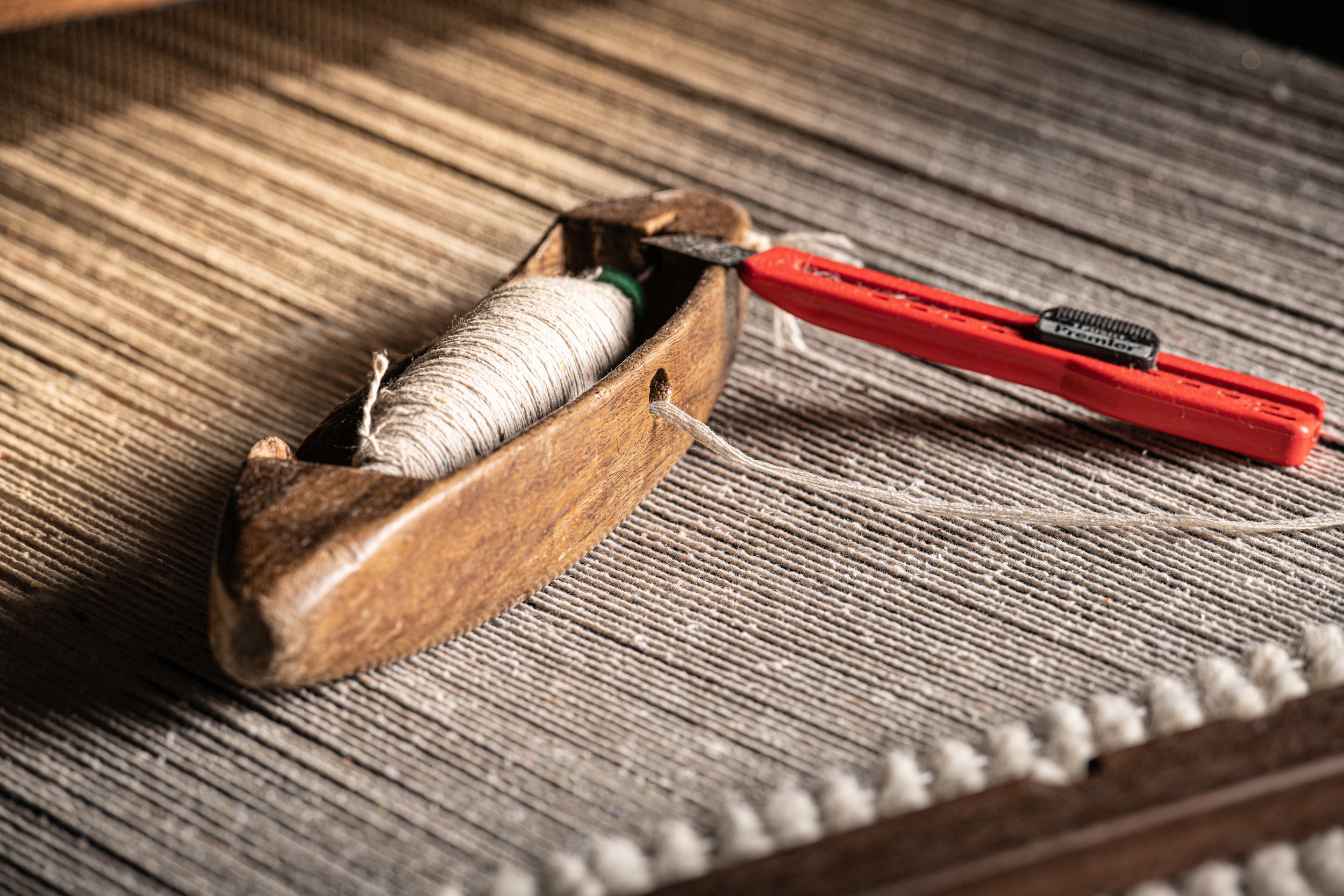
Our Story
Weaving Together Generations of Experience
Founded in 1921, Shabnam Textiles is a fourth-generation family business producing some of the world’s finest interior furnishing fabrics. We create meaningful textiles that elevate the beauty and treasured culture, inspired by our Indian heritage. Our textiles tell our stories in expressive imagery and soft, warm woven material.
Legacy Of Centuries
The making of Shabnam Textiles is the making of a legacy. The threads of our history reveal a colorful weaving together of long history of immigration and removal—centuries of heritage and tradition.
Our story can be traced to Abdul Rasheed settling down in the city of Meerut before the partition of India in 1947. Located in North India, Meerut, had been a centre of weaving since the arrival of Daryayi Baff weavers in the late 18th Century. It was here that Rasheed established Shabnam Textiles in 1921, immediately earning a reputation for high quality dhurrie and tapestries.Coming from a long generation of Ansaris (community of weavers by birth) Rasheed took great pride in his craftsmanship and considered weaving as more than a profession, more as an honorable and central component of his cultural identity.
Transitioning from Handloom to Computerized Loom
The legacy of Shabnam Textiles today is innovation, creating artful designs that spans the warp of weaving history and the weft of creative expression, from the very traditional to the thoroughly avant-garde. By transitioning from handlooms to computerized looms guided by modern design software, our artisans join trusted industry partners to bring our culture to the world. Every design is created in Meerut by our team of talented artists and woven from natural materials in the India.
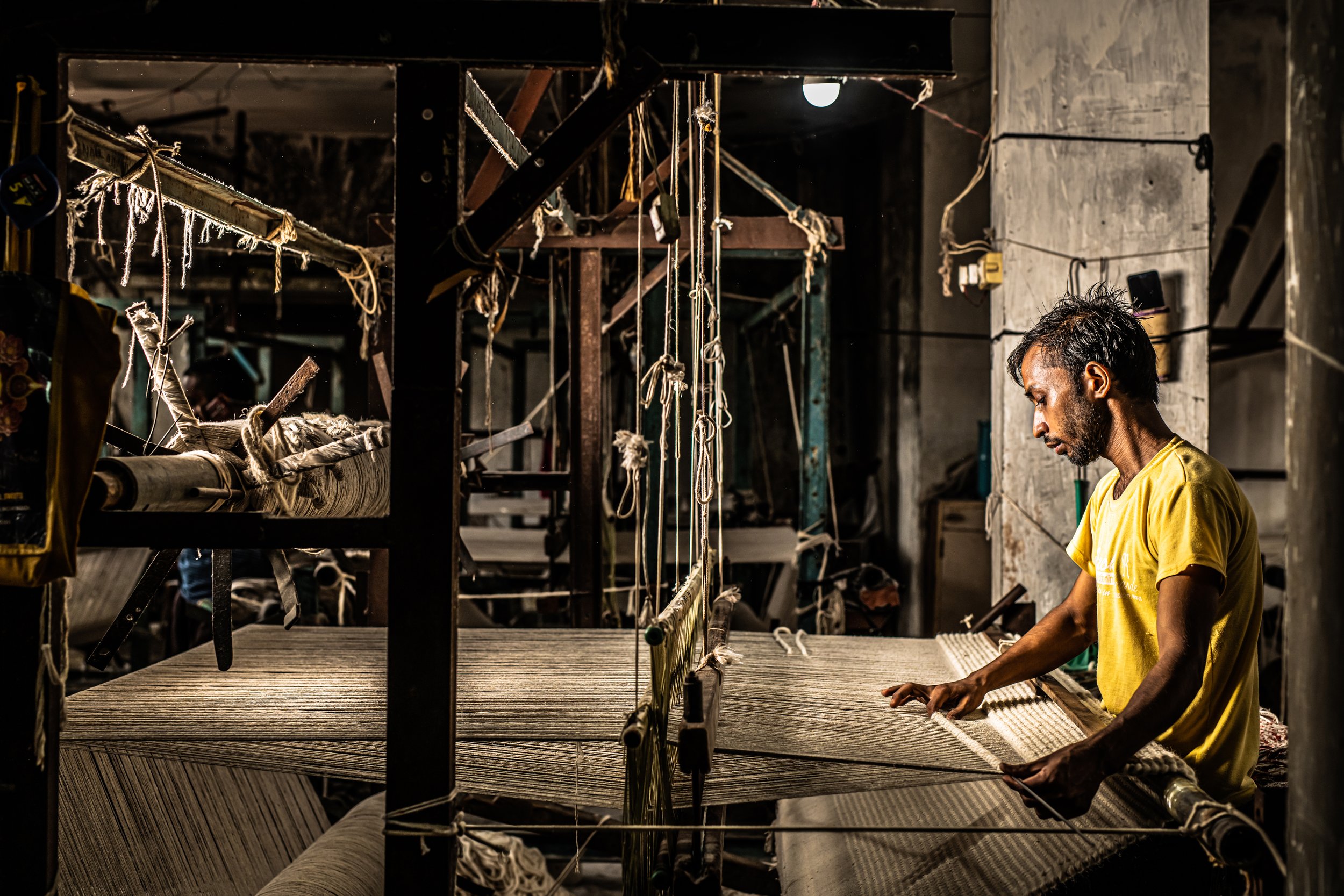
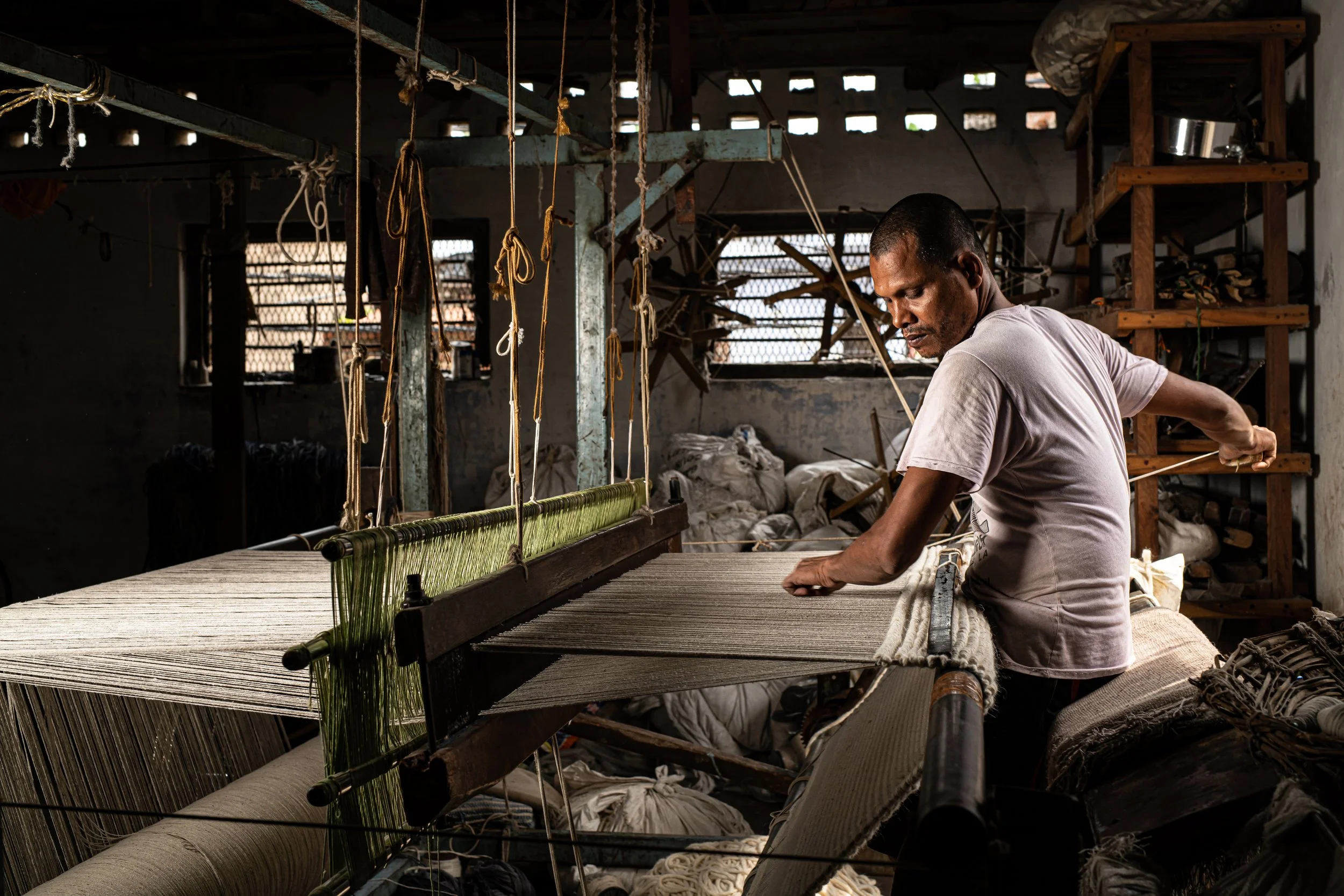


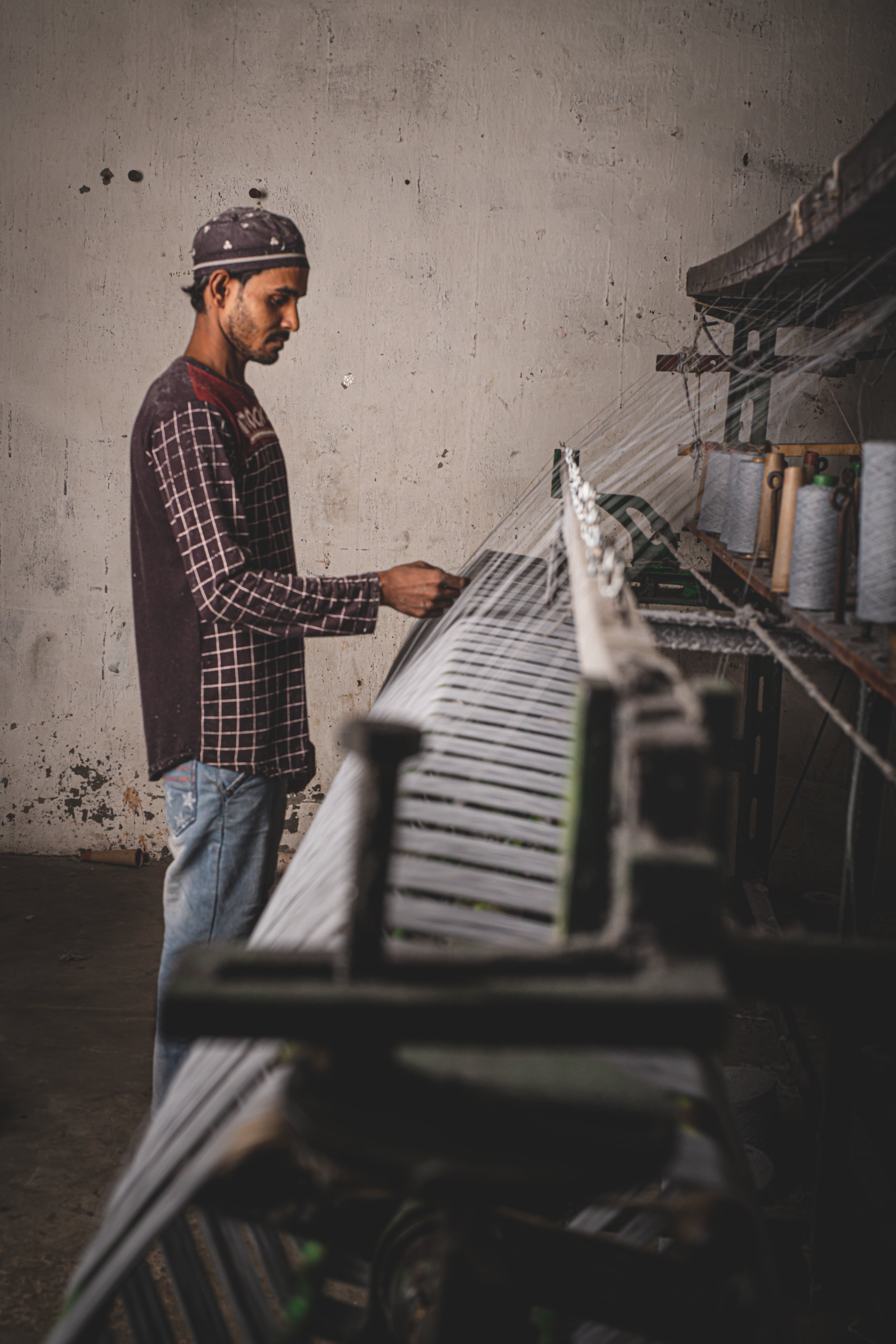

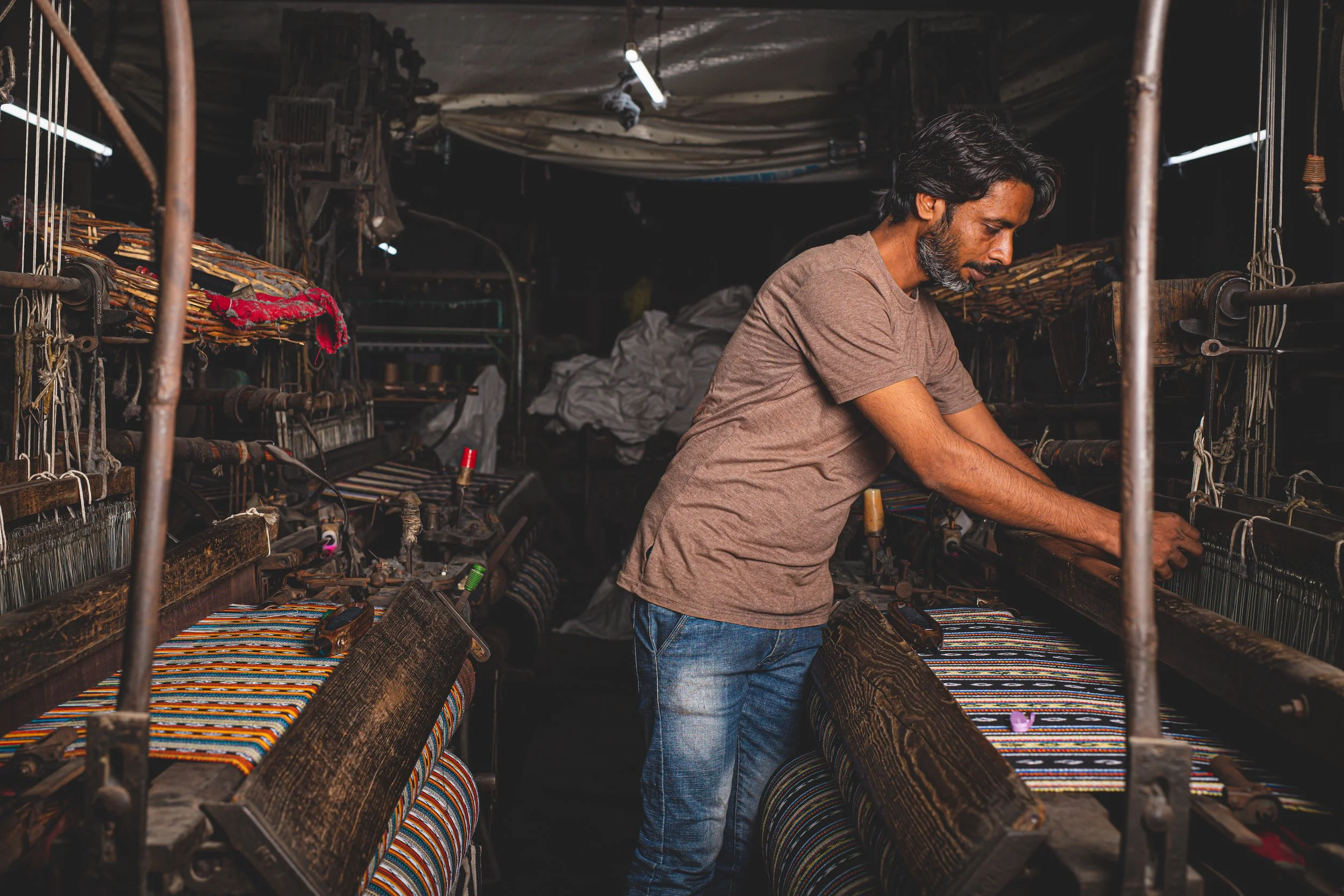
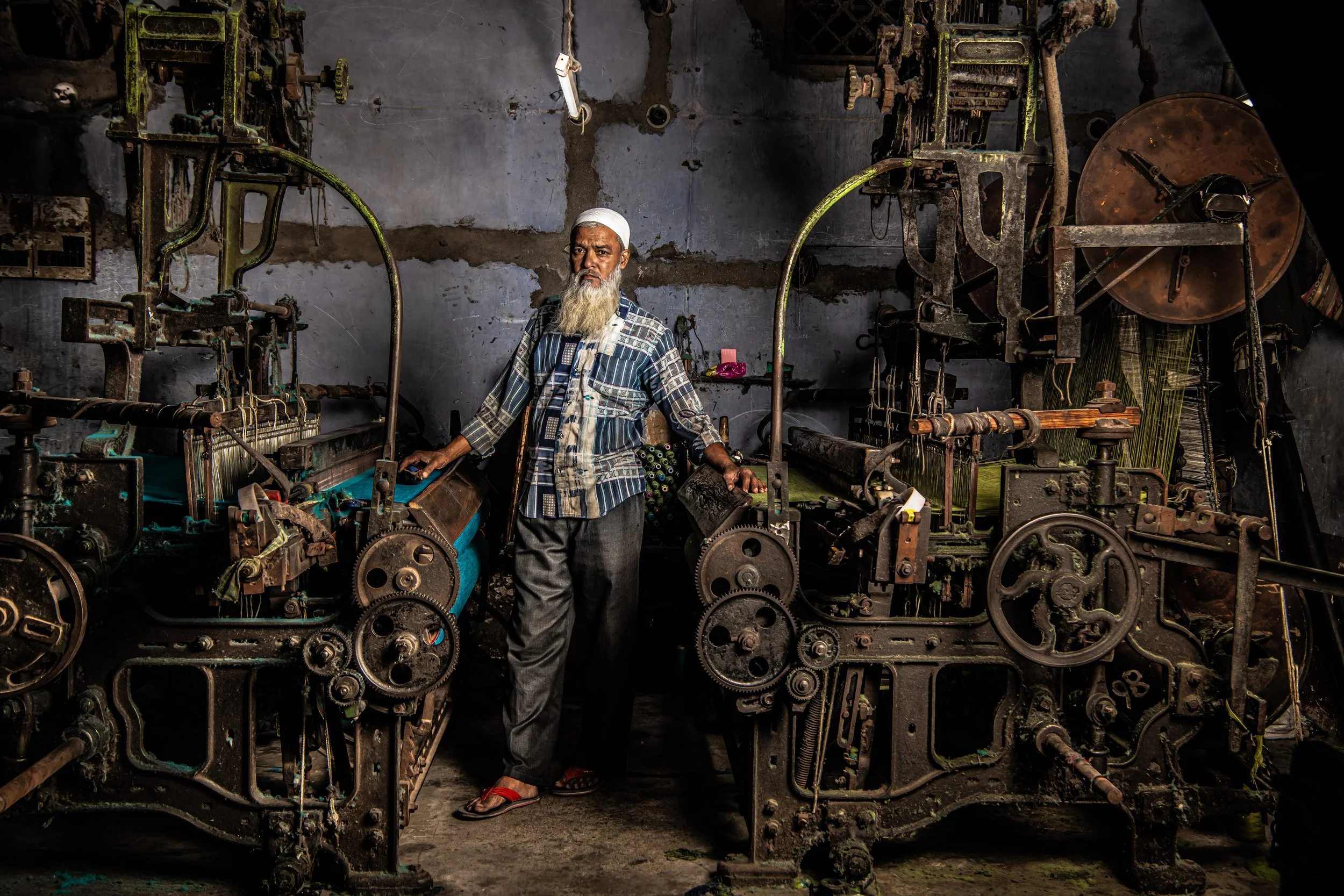
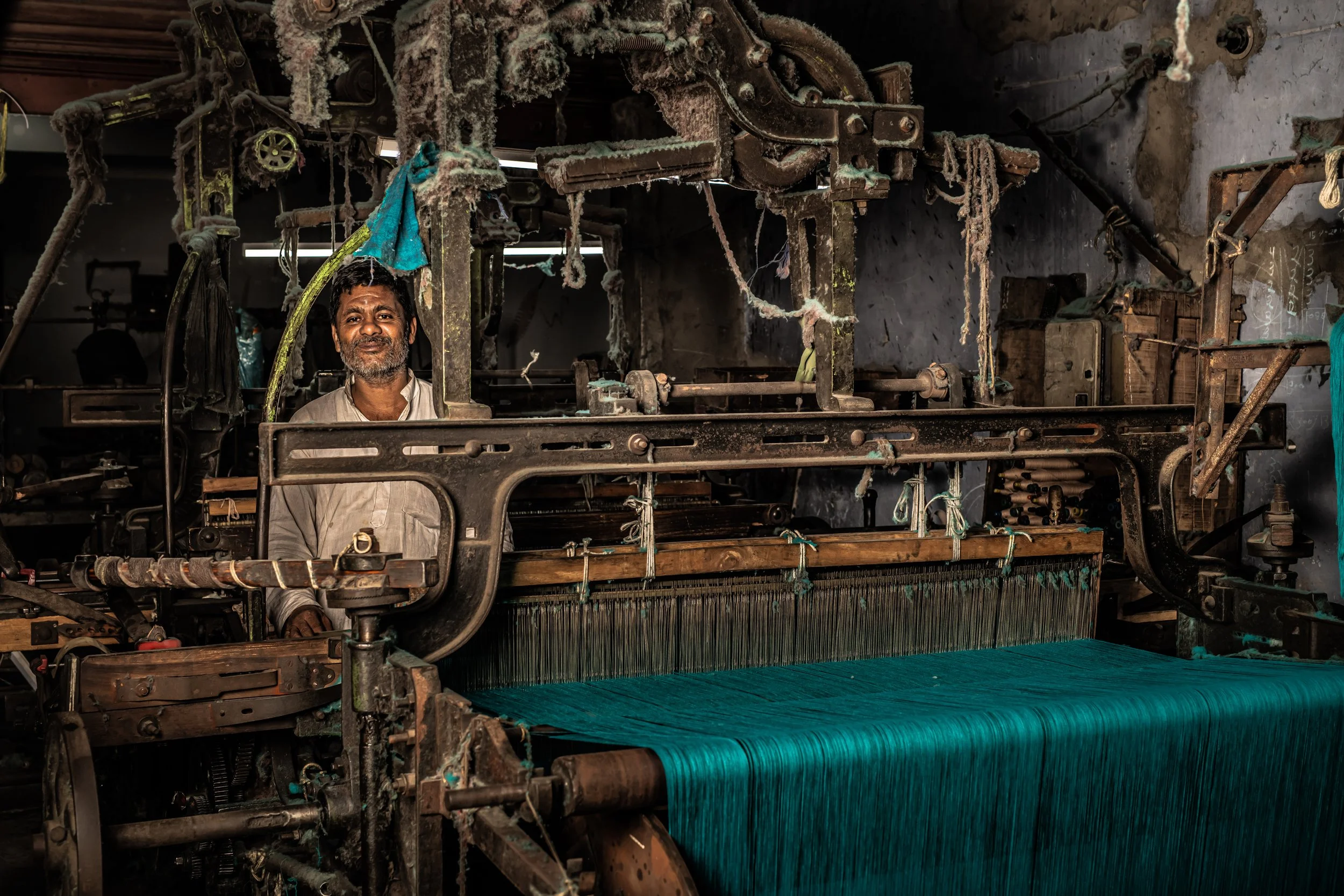
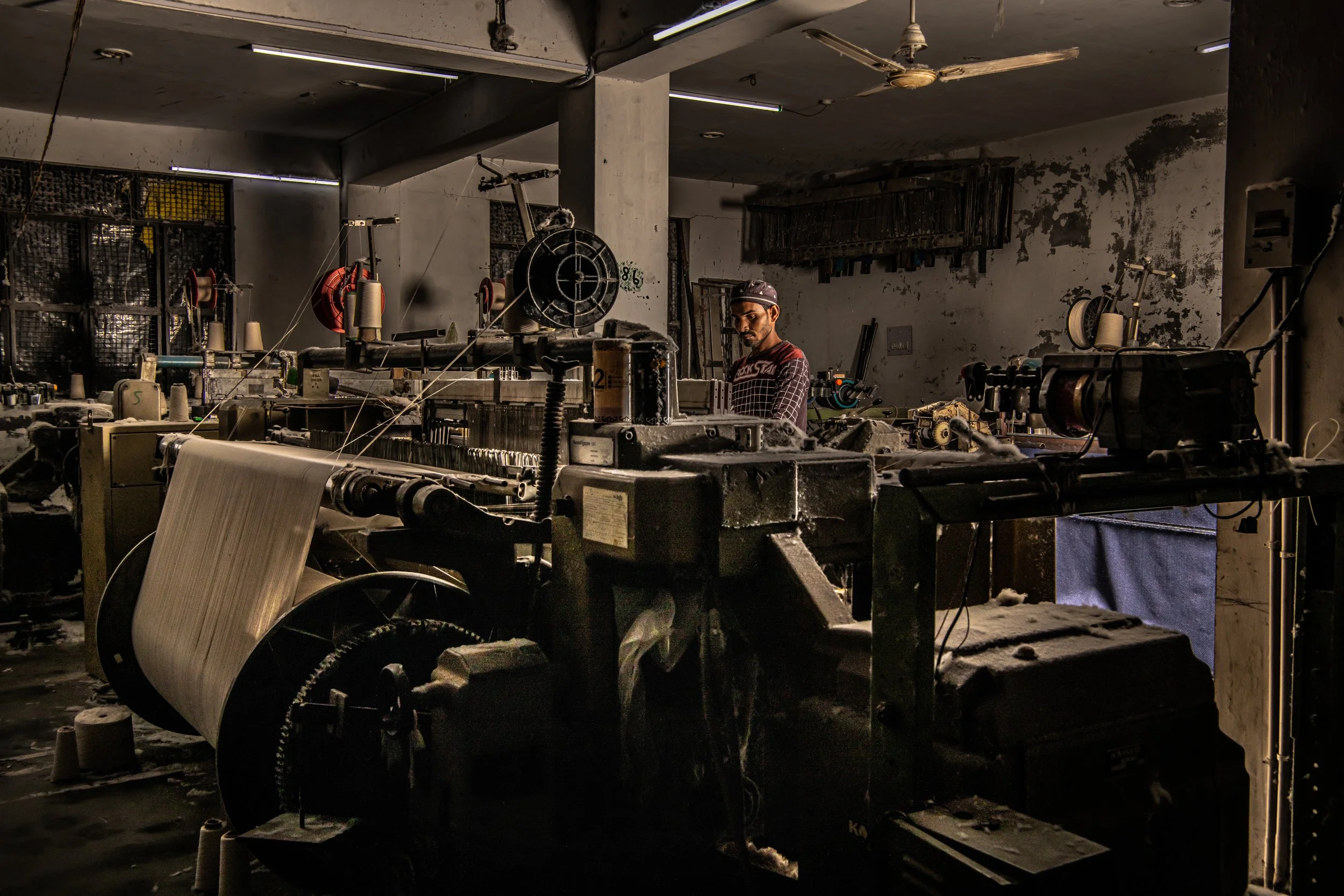
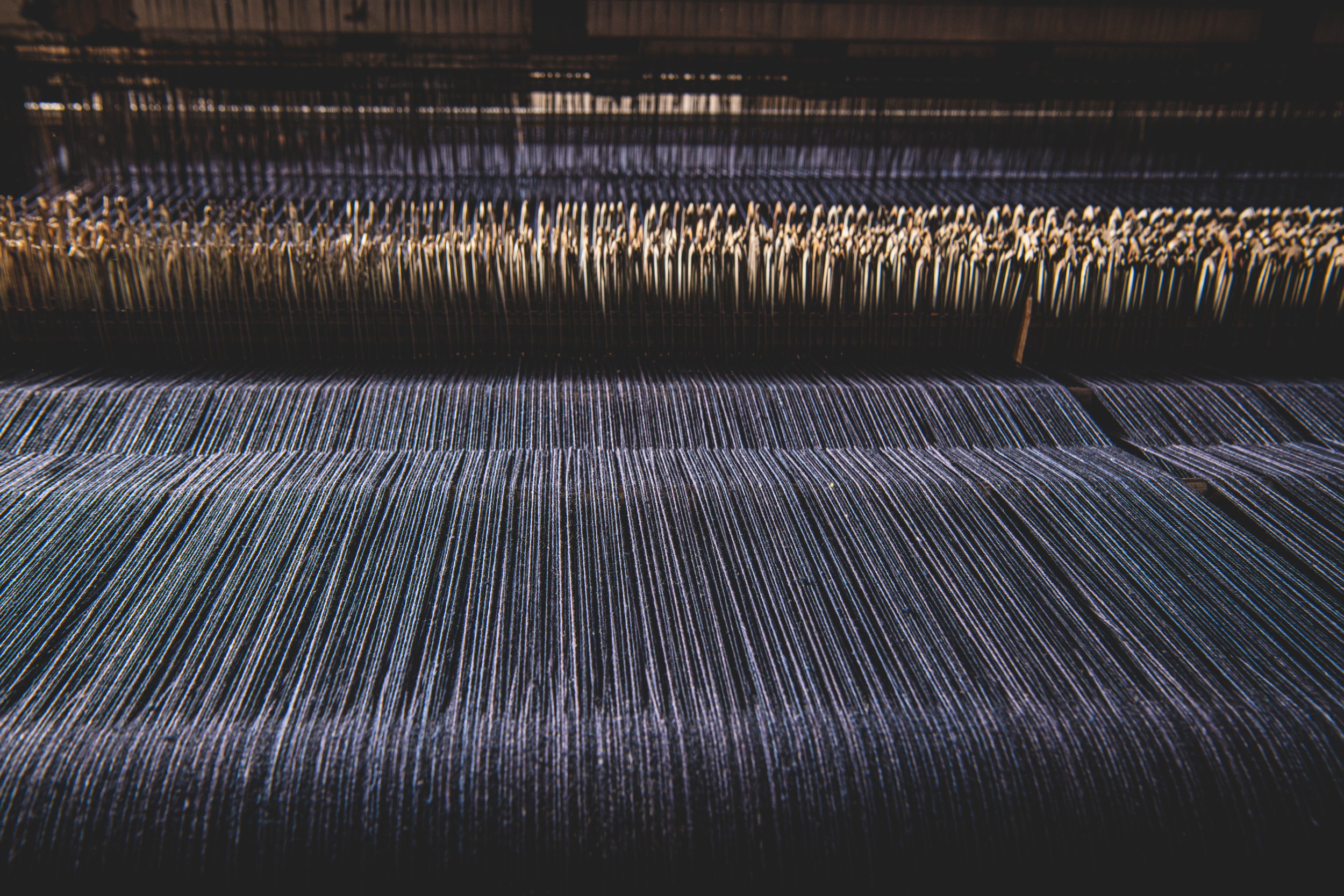
At Shabnam Textiles, we run two types of looms: handloom, traditional dobby equipped with modern rapiers looms. Dressing the loom involves the same process in all cases: a knotting machine is used to tie the new warp to the one in the loom, thread by thread, allowing the new warp to be pulled through the harness, ready for weaving.
On shuttle and dobby looms, the weft yarns have been wound onto pirns, which are loaded into metal-tipped wooden shuttles. These shoot side-to-side across the loom between the warp threads (in a gap known as ‘the shed’), with each passing of the weft pushed up against the previous one by a reed on the loom, allowing the design to be created. On the jacquard shuttle looms, the design is controlled by large packs of punch cards that either allow the warp threads to be lifted or to stay down, via an intricately-latticed harness; dobby looms are controlled by a system of pegs and lags that operate the shafts, which in turn lift the warp threads.
The rapier looms use cones of weft yarns, which are fed through tensioners and passed through the shed at high speed by bullet-shaped clamps, known as rapier heads. The designs are sent to the loom from our design department digitally, obviating the need for punch cards.
Once woven, all of our fabrics are painstakingly inspected and measured on a large, easel-shaped light table, to ensure that they leave us in immaculate condition, wherever in the world they are destined.